Painted in iconic purple and yellow, the KW Suspension factory was hard to miss! The complex sprawled over several acres with over 23,000 sq/m of operating space and was home to an efficient crew of around 200 employees. We were greeted by Christian Schmidt, the companies head of PR, who would be our gracious tour guide for the visit. The first thing you notice is a cup racing prepped mid-nineties Honda Accord sedan! The ‘well raced and worn’ car seemed out of place as the only vehicle on display in the world’s premier aftermarket suspension company’s lobby. However, it is one of the most important artifacts in KW’s heritage.

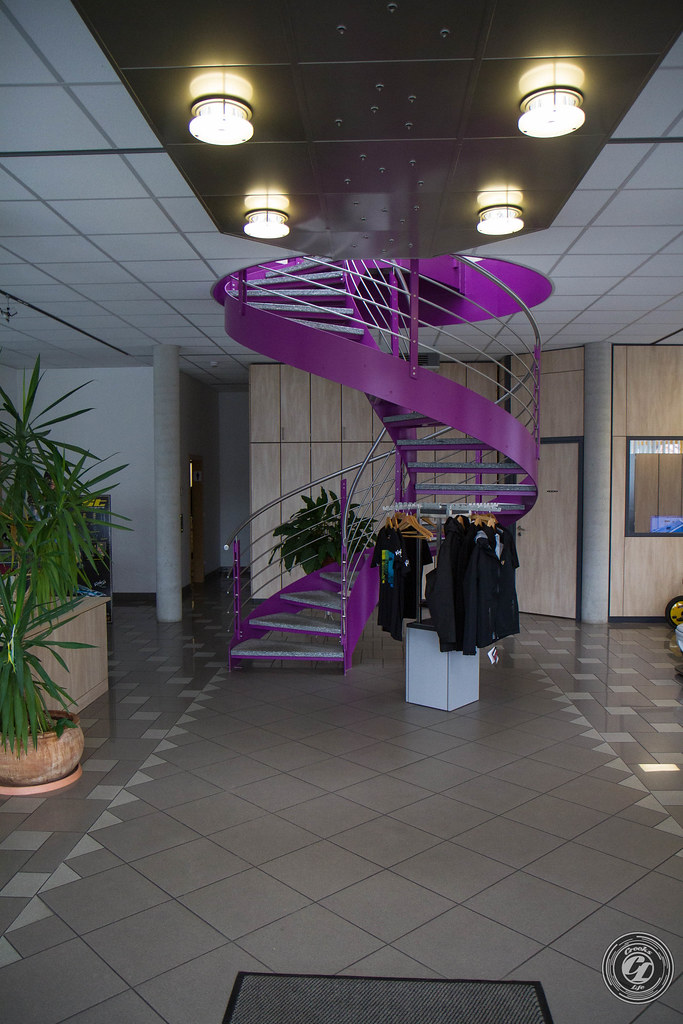
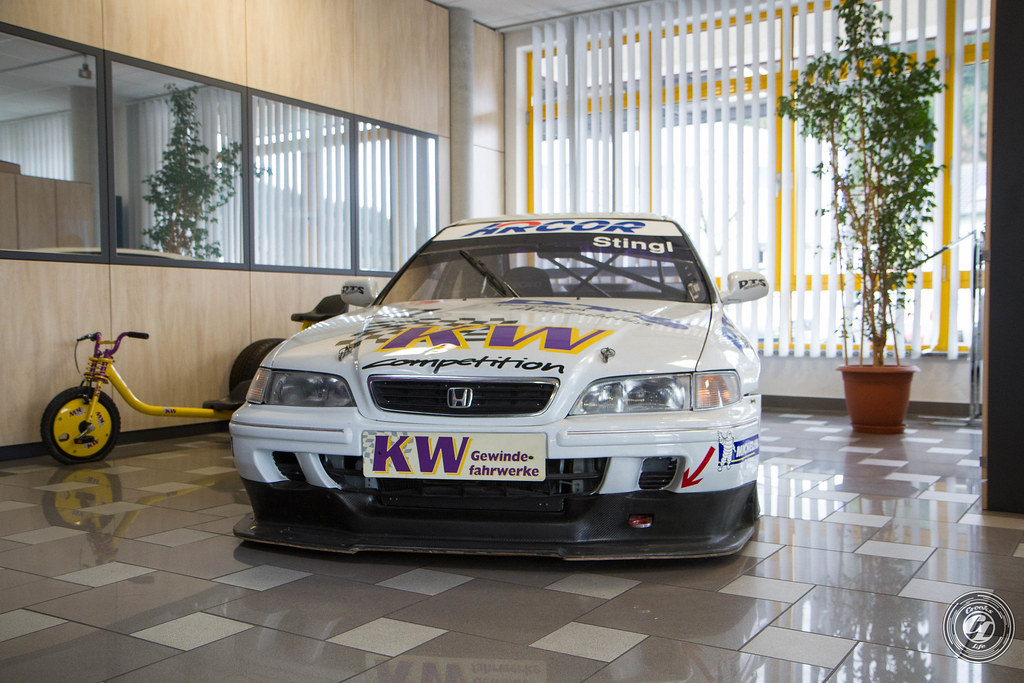
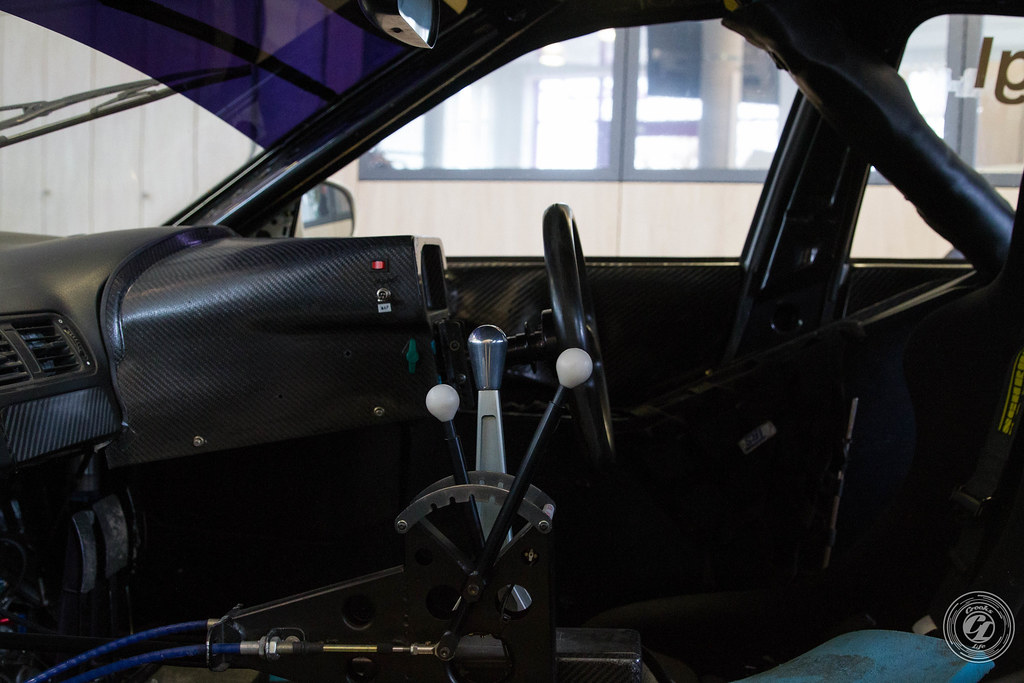
The Wohlfarth brothers, Klaus and Jurgen, (Klaus Wohlfarth’s initials being used for the company name) were racing in the clubsport class of the German circuit with an old Opel C Kadett (Buick Opel/Chevy Chevette) in the late 1980s and early 1990s. They were tired of the limited spring and strut suspension options available on the aftermarket at the time so they decided to embark on a venture to produce a fully adjustable spring strut combo (coilover) which had been used in professional racing for years. The brothers along with their friend Thomas Wurst, who was an engine builder, created the first coilover system to be approved by the German government (TÜV) for use on public roads. In 1999 they entered their shop car, a Honda Accord sedan equipped with their TÜV approved adjustable suspension, into the DTC Series with great results (2x Pole Position, many Top 3 finishes). After their debut season as a humble three-man shop with street approved racing suspension, KW went on to become one of the top names in aftermarket sport/racing components.
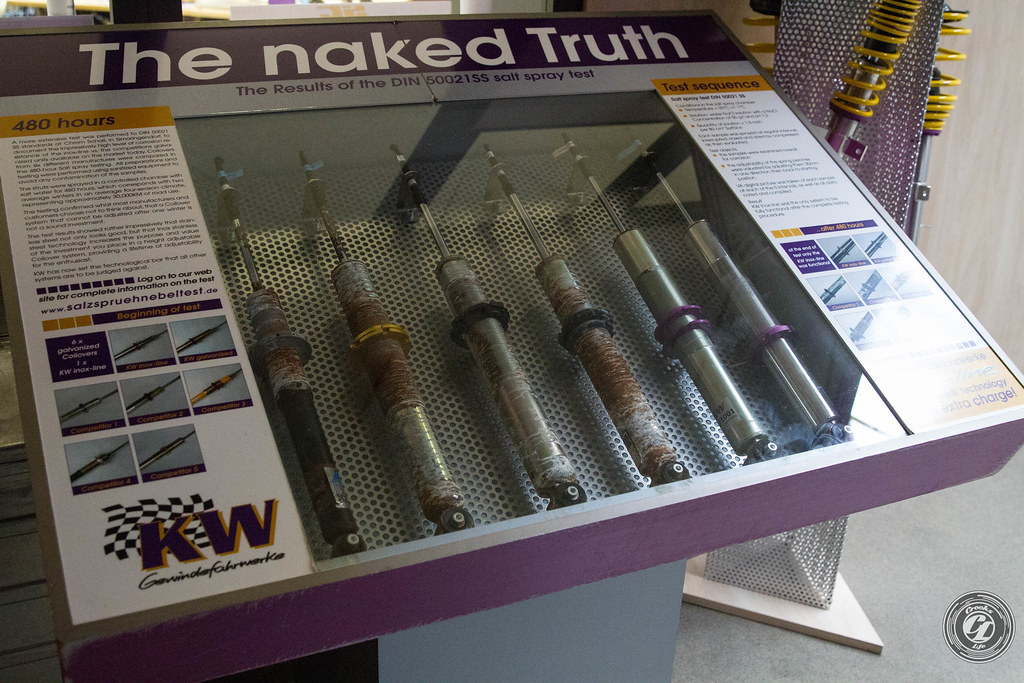
A display showcasing how KW's stainless steel construction holds up over prolonged use compared to competitors
From the lobby, Christian showed us through the company’s proprietary research and development section full of CAD drawings, computers with suspension designs, and prototype parts for the next generation of KW innovation. The next stop was one of the company’s prized possessions; a 1/15 in the world ‘7-post drive dynamics’ rig, which is normally used by Formula 1 race teams. This impressive hydraulic apparatus allowed KW engineers to send cars through test profiles of various race tracks and street conditions to fully characterize the cars’ vibration, weight distribution, compression, rebound, and many other factors. All of which will affect the expert and purposeful design of KW’s products for the car.


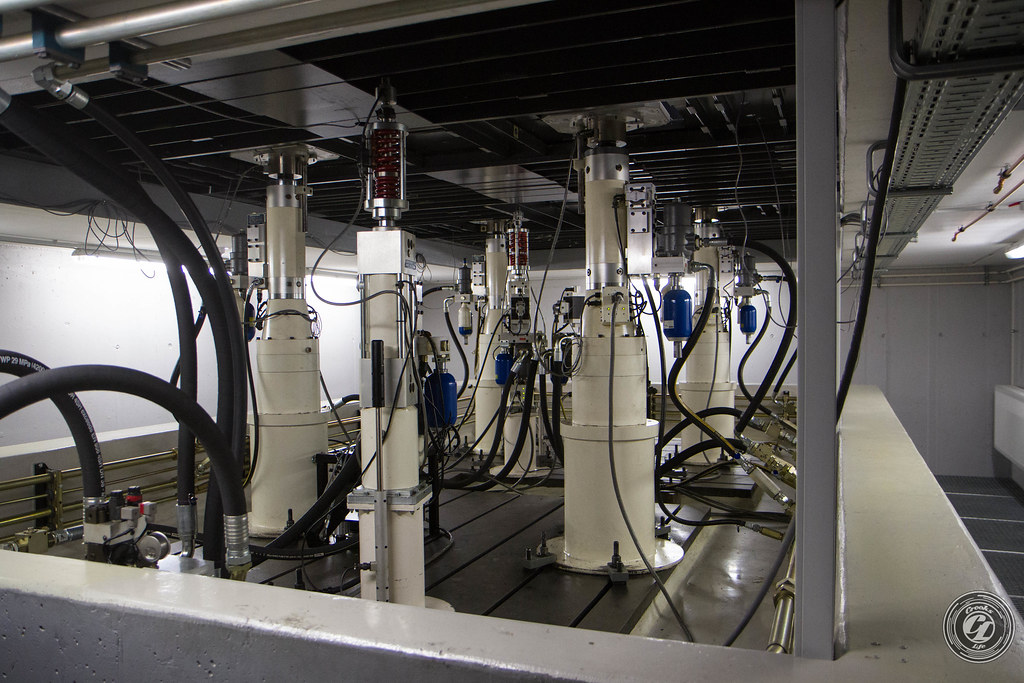
Up next was raw material storage and milling where we got to view the birthplace of all KW struts. The building was full of active milling machines and workers. The struts would enter the building as raw stainless steel rods. They are hallowed and shaped and threaded for the adjustable spring. Next, they are set in a model specific jig to have the mounting hardware and caps hand welded into place. They were then stored and sent off for refinishing.


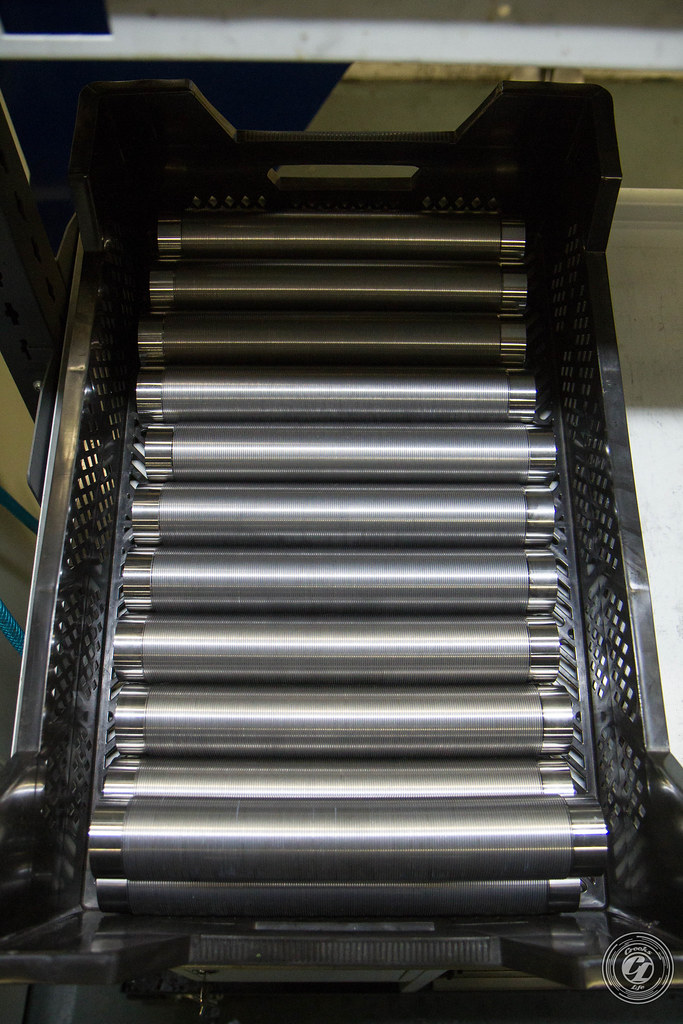
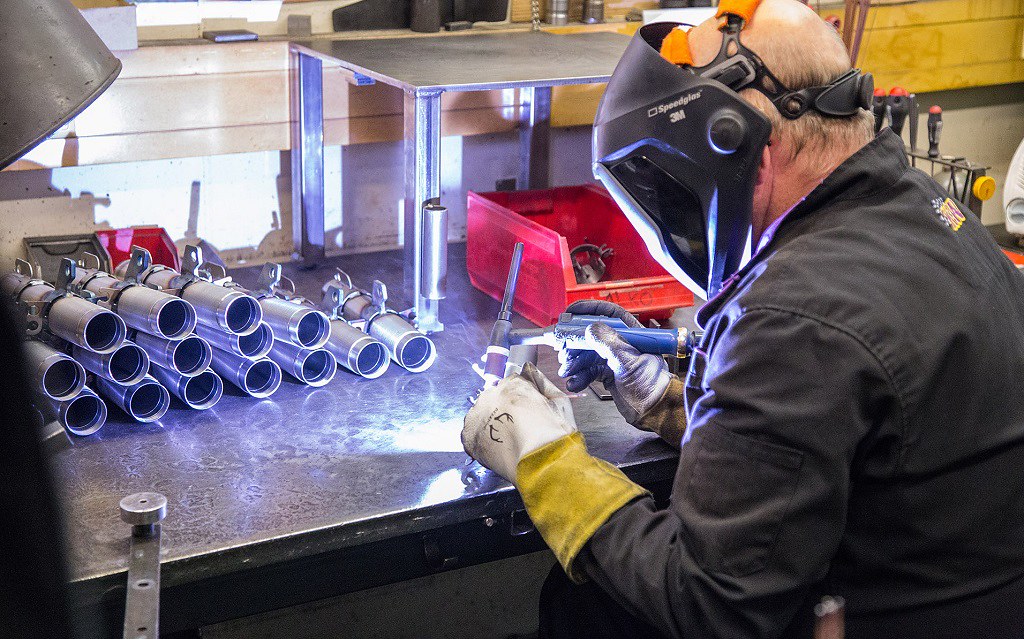
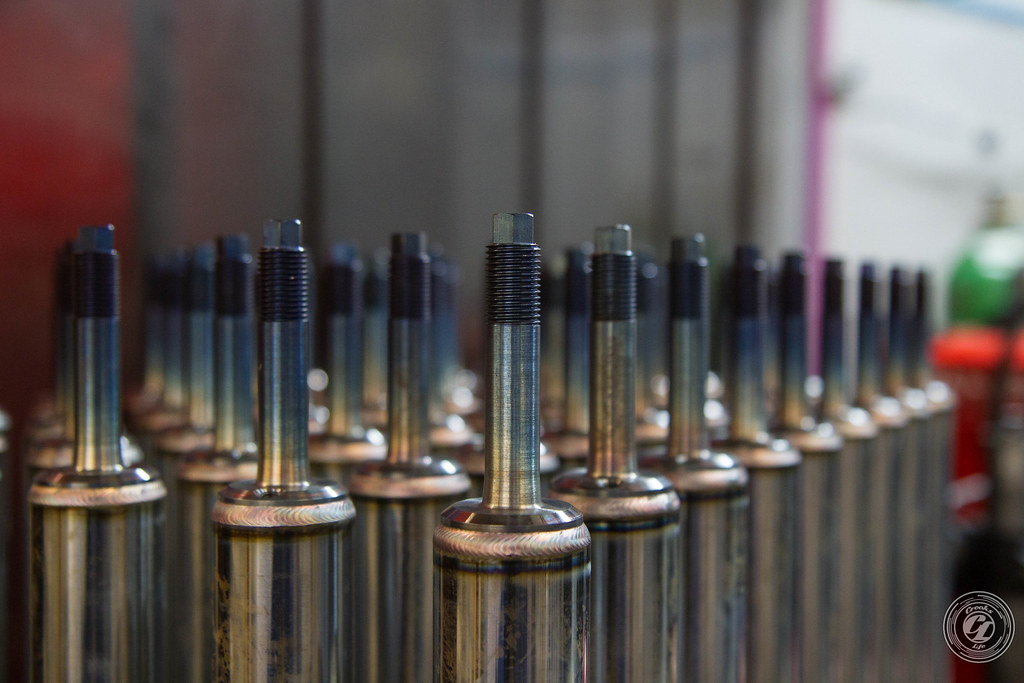
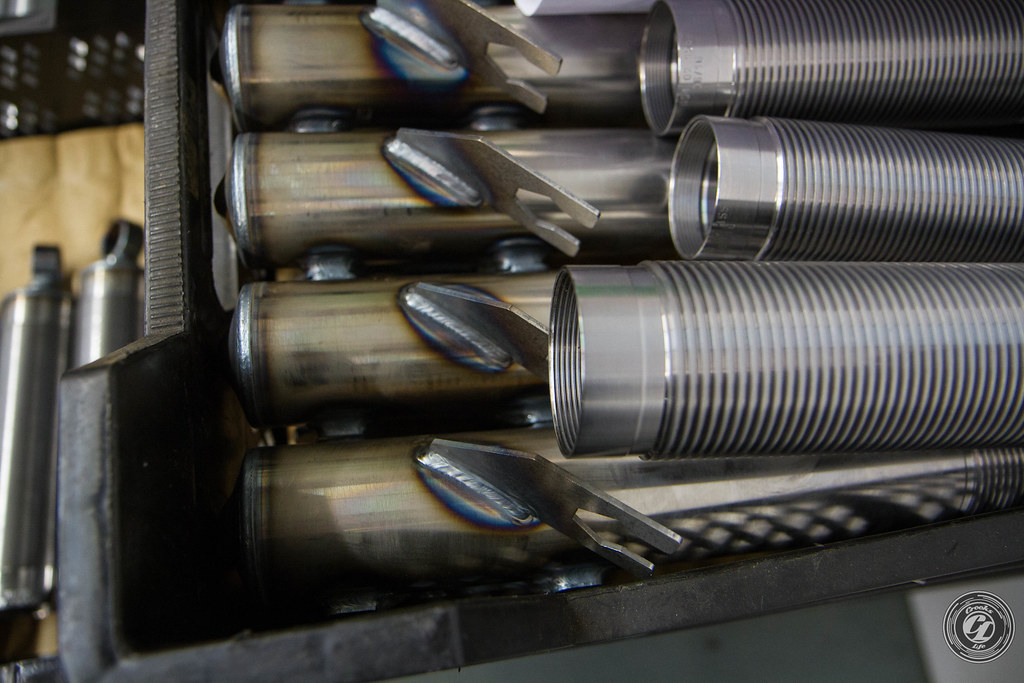

Moving on, we entered the building where the struts/dampers were assembled. On the second floor the refinished parts made their way through several working stations that assembled all of the interior components of the adjustable struts/dampers like the KW V2, KW V3, KW Clubsport, and adaptive KW DDC. Every station had precision equipment that ensured measurement and pressure specs were within tight tolerances. Once the strut was fully assembled, it was hooked up to a hydraulic machine that compressed and released the strut at various speeds, once again, ensuring the strut was within a hair thin specification throughout the entire profile. When the strut passed the compression test it represented the finished KW Suspension product from a fabrication standpoint. The struts were loaded into crates and sent to the bottom floor for storage.
The bottom floor was a massive warehouse that housed all components needed for assembling finished suspensions for thousands of different configurations. Workers would place the various parts needed for a small production run in trays as batches. An automated machine the size of the building would then whisk the tray away to storage. Whenever market demand called for another production run, the workers would simply dial in the model number and the machine would magically pull out the tray with the required parts. The trays of parts were then sent to the building next door to be hand assembled and packaged.
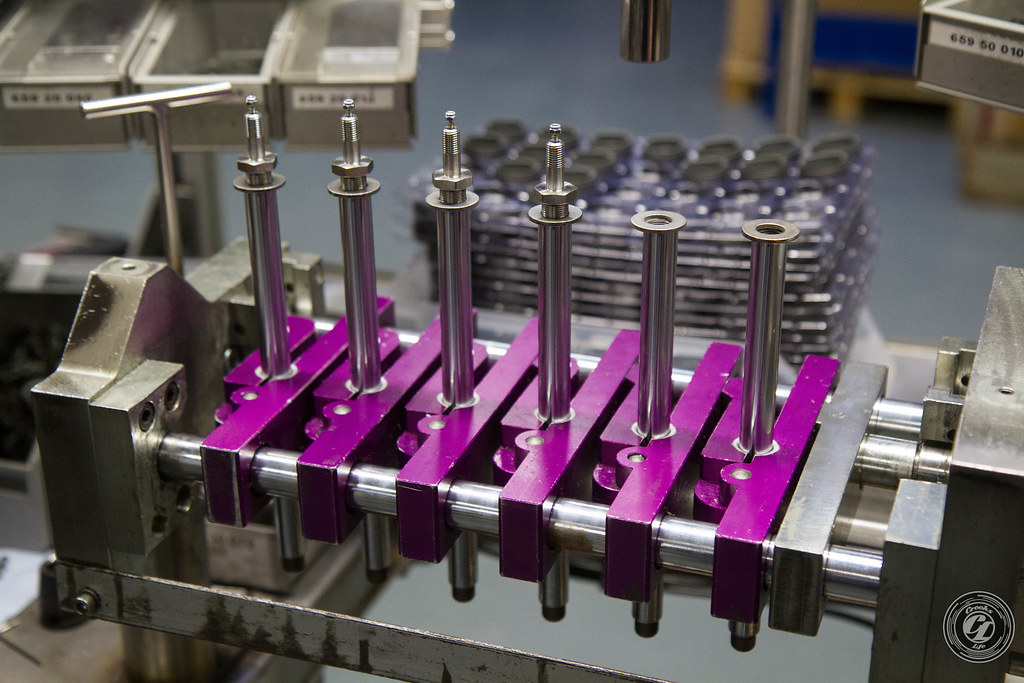

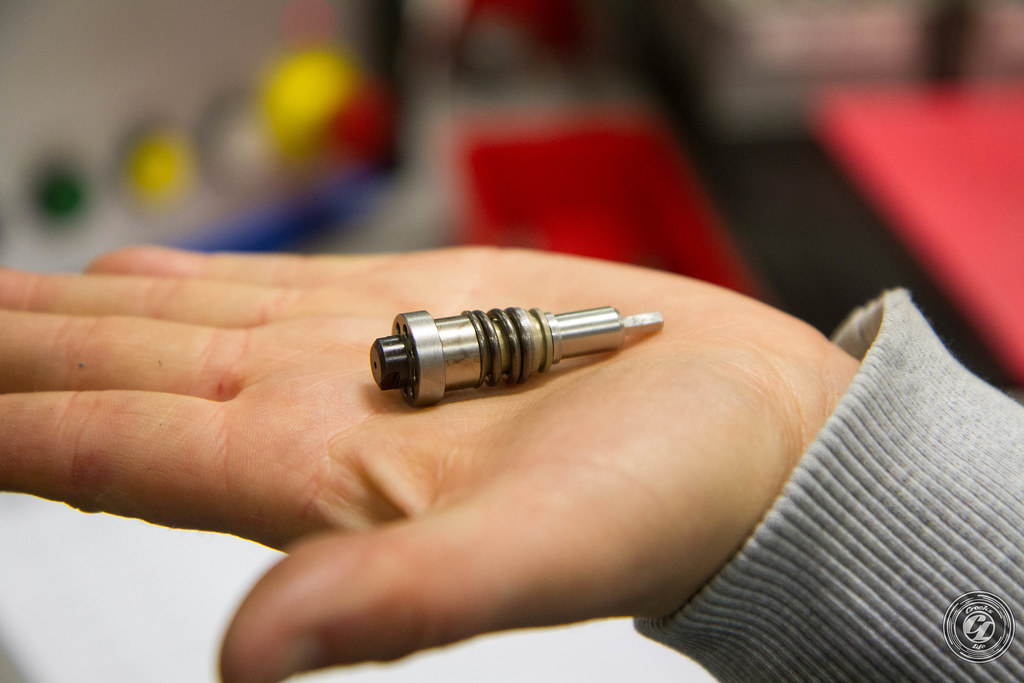
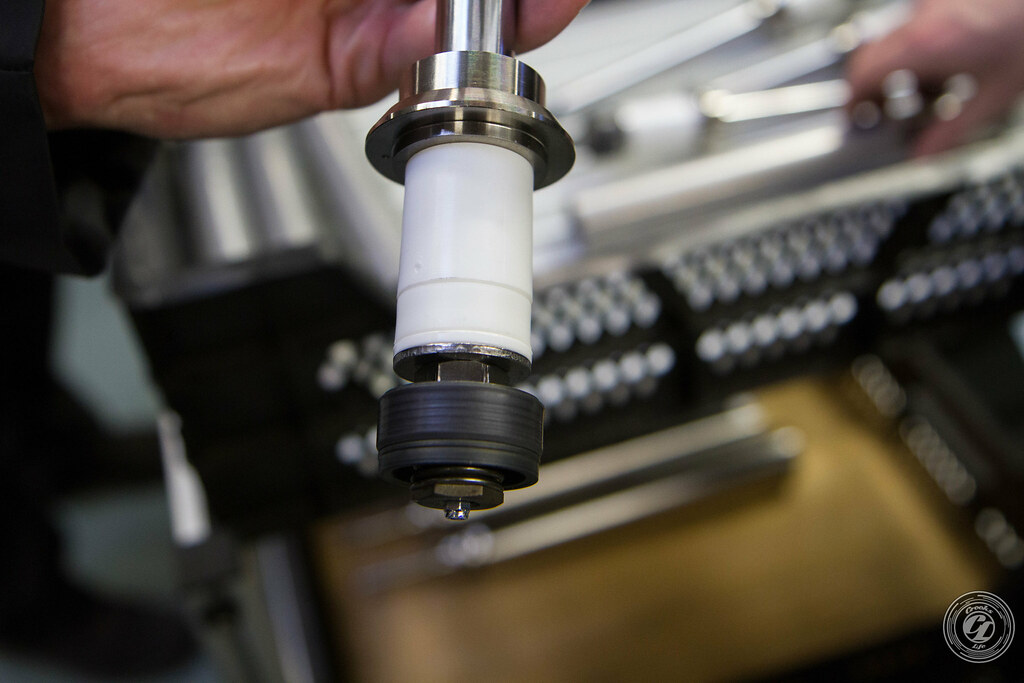
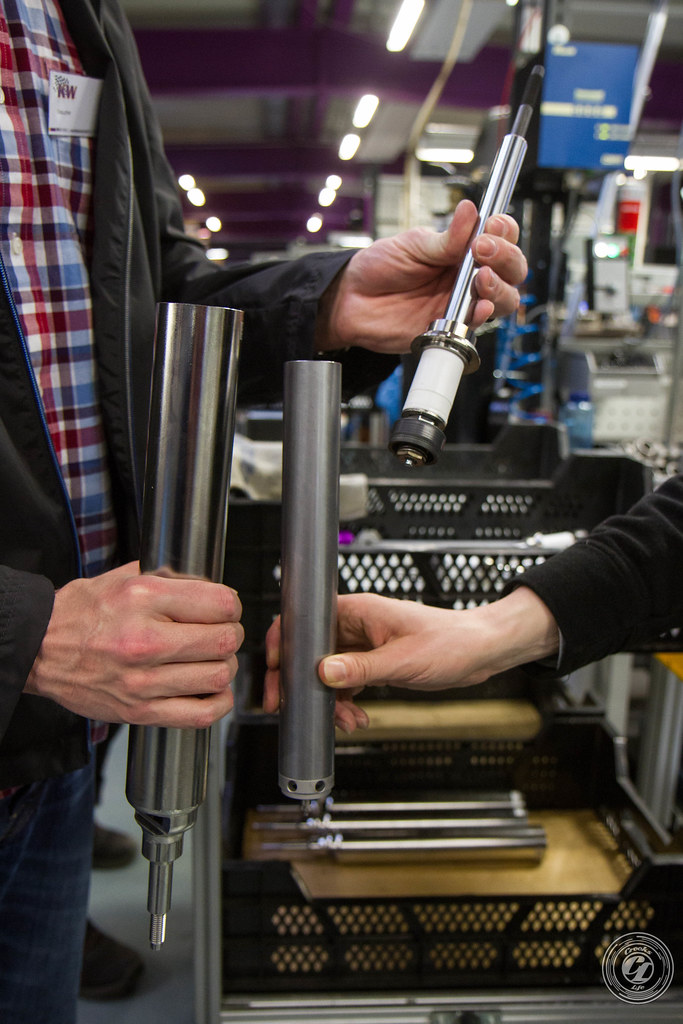
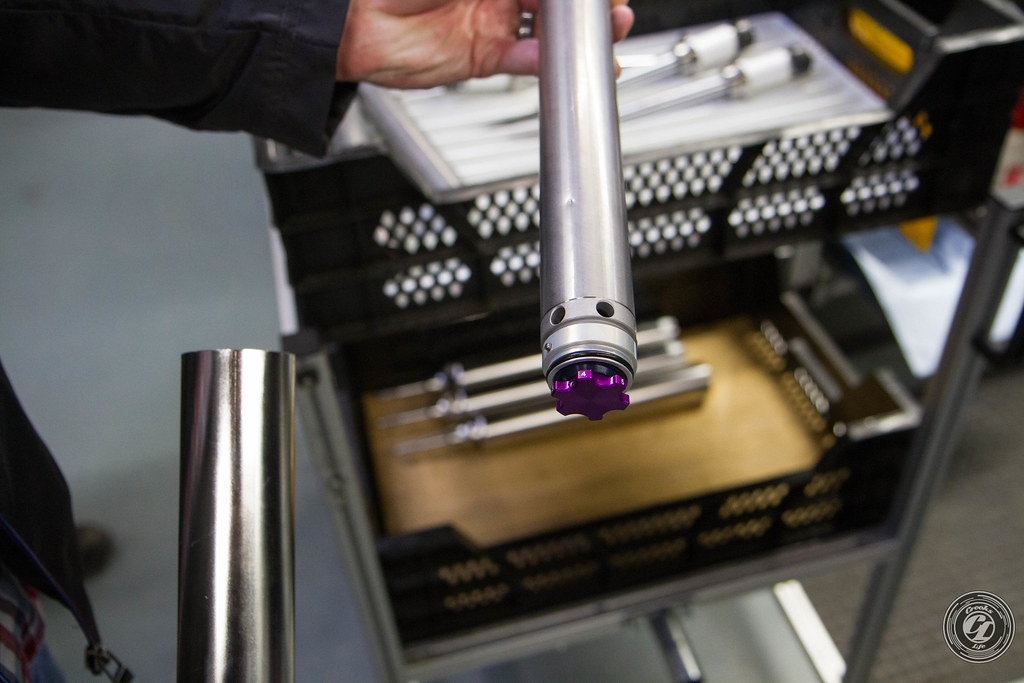


KW outsources the springs used in their kits because it is more cost effective for them to design the kit to a specific spring rate and simply order springs that match that spring rate from their suppliers. KW’s only change to the spring is powder coating it the iconic KW yellow! The springs are then sent to the final assembly and packing building where they meet with the struts and other components to be hand made into the final product. In assembly line fashion, the individual parts are all assembled, labeled, cleaned, and packed into their boxes and palletized for daily shipments all over the world!
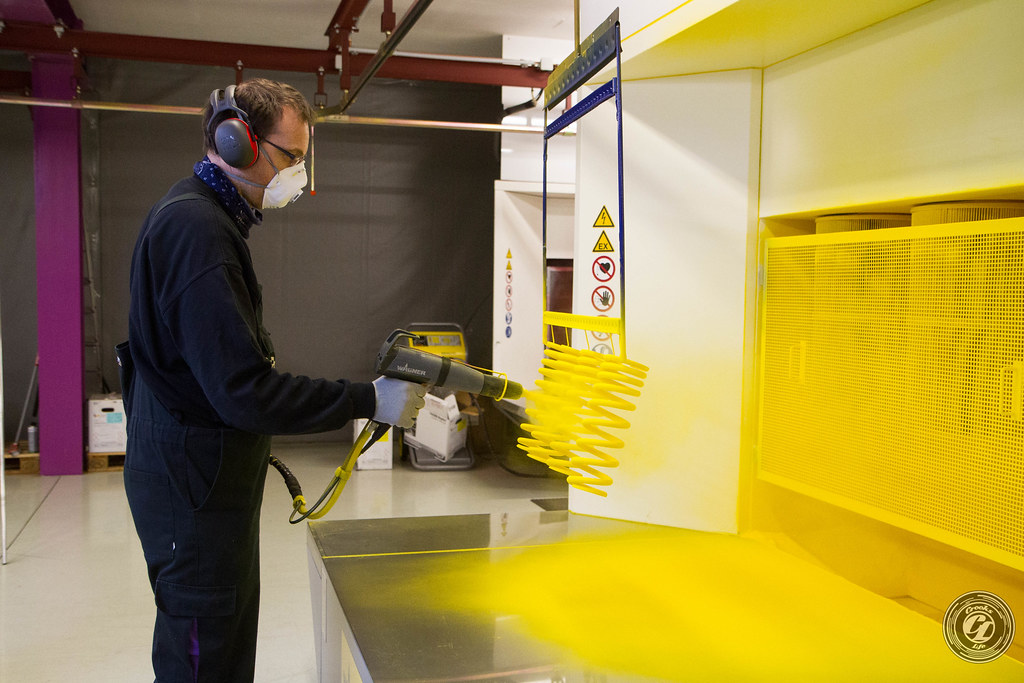


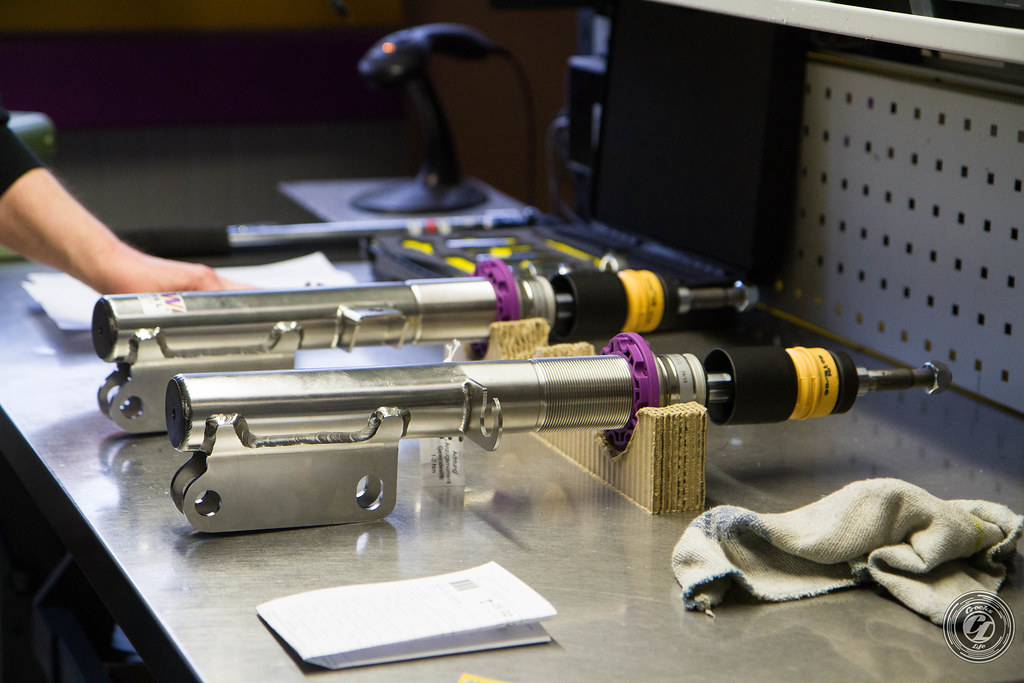
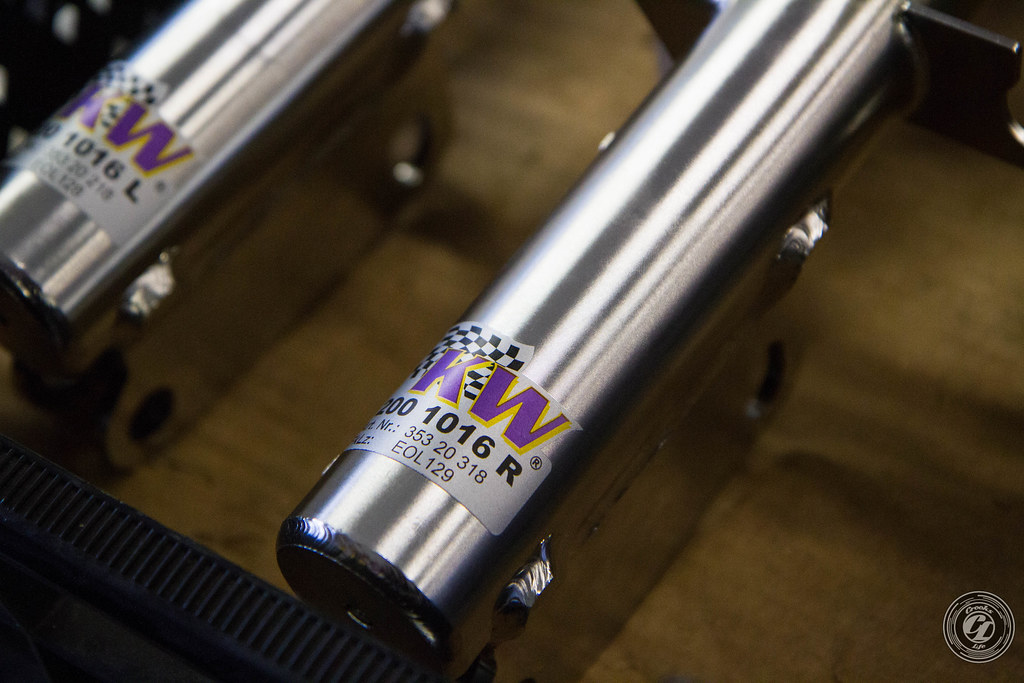
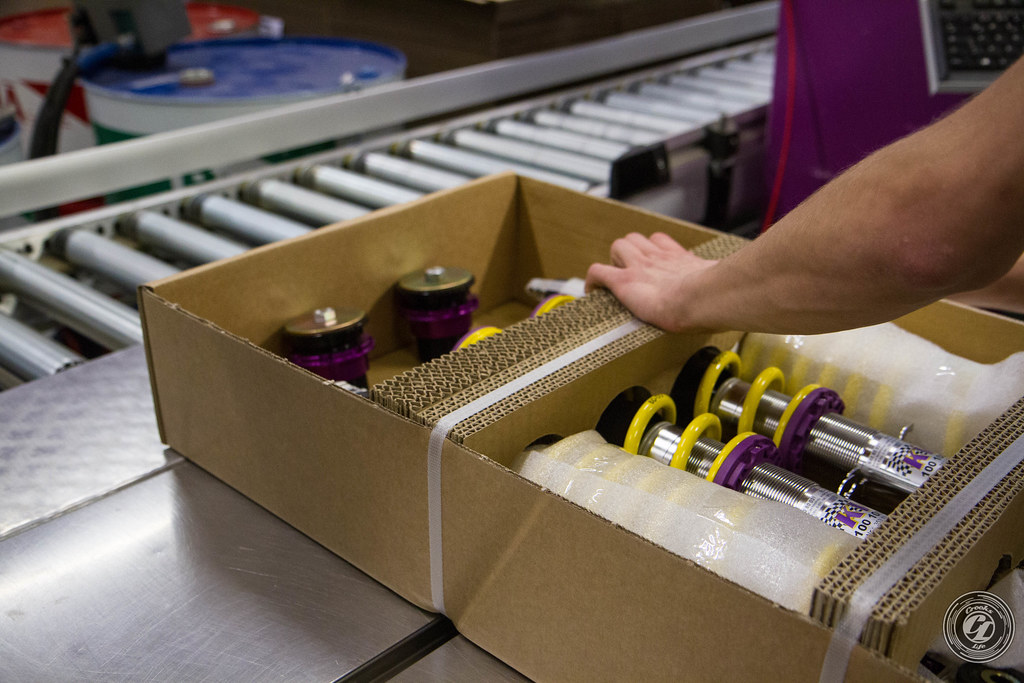
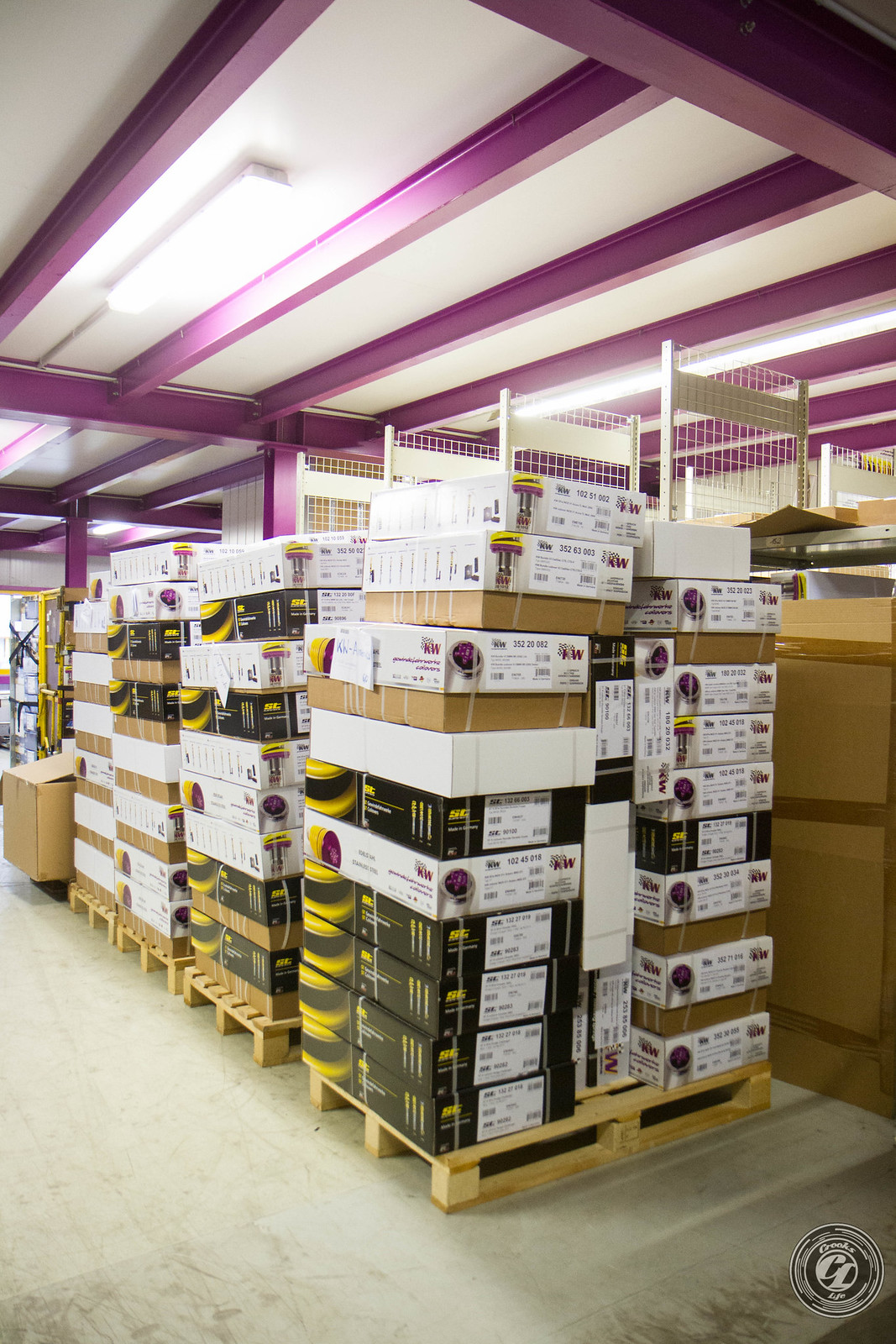
Jimmy and I definitely gained a new appreciation for the process involved in designing and producing suspension components. From countless hours of characterizing vibration behavior of individual vehicles, using that data to design the perfect combination of spring rate, rebound and compression, and then testing multiple iterations of the design until it’s perfect! To the skilled workers of the KW factory who hand weld, assemble, and test every single production kit! The quality of design and care of hand-assembly shows in every KW suspension product.
We were very fortunate to be offered this rare look into the inner workings of an innovative and successful leader in the aftermarket suspension market. I hope that readers enjoy this write up and photo journal as much as we enjoyed producing it. Needless to say we have a new respect of the KW products on our cars and look forward to many years of driving pleasure with their suspensions in the future.
--Curt2000
Bookmarks